The digital threat landscape can be a battlefield. Hackers’ tactics are constantly evolving, and traditional security measures often struggle to keep up. Artificial Intelligence (AI) and Machine Learning (ML) are powerful allies in the fight for resilience. From predictive analytics to response and mitigation, this post will explore how these technologies can bolster cybersecurity strategies.
The Evolution of Proactive Defense
Vulnerability management assessment (VMA) and penetration testing (pen testing) are critical to a proactive cybersecurity strategy. The traditional reliance on manual scans and analysis meant these processes were slow and tedious. AI and ML are changing that.
With the ability to quickly analyze vast amounts of data, AI and ML enable accurate threat prediction, prioritization, and mitigation. These models can continuously learn and adapt to new threat intelligence and dynamically respond to the rapidly evolving threat landscape.
Behavioral Intelligence
Today’s cybersecurity measures must account for the rise in interconnected systems and devices and the new opportunities to exploit human fallibility inside this environment. Focusing on external threats alone isn’t an option.
User Entity and Behavior Analytics (UEBA) leverages AI and ML to identify a broader range of threats– such as inside actors, social engineering, and brute-force attacks. By continuously analyzing user behavior patterns, anomalous activity detection is honed and accelerated– allowing for more informed preventative action and enforcement of regulatory compliance.
Answering Alert Fatigue
Teams are often bombarded with cybersecurity alerts– many of which can be false positives– leading to alert fatigue, wasted resources, and delays in addressing critical threats. These delays can trigger cascading security breaches. AI and ML can streamline this process by filtering out false positives, automating threat responses, and highlighting the most critical threats.
Automated responses can address low-risk alerts, block malicious access attempts, and quarantine compromised devices or networks. These measures can minimize the damage of cyberattacks and enable human experts to focus on higher level initiatives and high-priority incidents.
The Takeaway
The future of cybersecurity is inextricably intertwined with AI and ML. As these technologies continue to evolve, so too will their ability to detect, prevent, and respond to cyber threats. Empowered by AI and ML, security teams can proactively safeguard systems today and prepare for the ever-evolving threat landscape of tomorrow.
Ready to learn more? Contact us today to schedule a no-cost consultation.
We empower our clients to build safe, sustainable operations by delivering comprehensive Operational Technology (OT) solutions. From concept to implementation and beyond– we'll be there every step of the way.
Let's collaborate.
Schedule a no-cost consultation today.
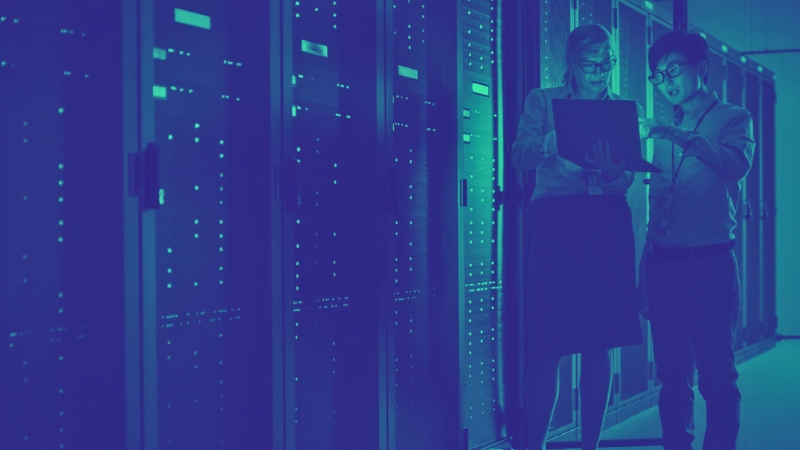
more on our website
Industrial Cybersecurity
More Posts