While everyone is familiar with the term “IT” (Information Technology), the term “OT” (Operational Technology) is far less familiar to the general public. That is not to say OT is newly emerging; quite the opposite. Over the last two decades, IT and OT have begun to converge. You’ve likely heard terms like “IIoT” (Industrial Internet of Things) or “Industry 4.0.” But there are unique differences that set OT apart from IT.
Production
While IT is extremely important at the corporate (or “Enterprise”) level, OT is the livelihood of any facility. The mission of any OT system is to achieve the greatest production output with the least amount of downtime possible.
Since production is the livelihood of any industrial facility, so too are the operational systems that keep them moving. Loss of production for any reason has a direct impact on a company’s bottom-line. Whether due to an outdated, unreliable platform, poor configuration, unprepared support staff, or insecure technology allowing for system breaches – many factors can affect production. Be sure to utilize an OT specialist with the experience to reach your maximum production output.
Safety
IT and OT must both be vigilant in mitigating security risks. However, IT’s risks generally lend themselves to trade secrets and corporate accountability. OT’s risks can be much more tangible: Unsafe operating conditions or monitoring can result in health and safety issues such as fatalities or environmental catastrophes.
In past years, many have taken the “air gap” approach to securing their OT control systems – keeping any production equipment separated from Internet-connected Enterprise equipment. In theory – and in a time before flash drives and smartphones – this was enough to mitigate operational risks. But, as consumer technologies emerged, so too did many large-scale security breaches affecting Industrial Control Systems.
Air gapped systems that were not physically connected to the Internet would run on outdated security patches because they were seemingly “secure.” With the advent of devices like flash drives and smartphones, however, control systems around the globe became vulnerable. Cyber-attacks could now halt production, disable critical safety systems, or result in catastrophic loss simply by altering production readings.
Having a team of Globally Certified Cybersecurity Experts at your fingertips is now vital for any industrial environment.
Skillset
While the fundamental principles of IT networks are shared with OT networks, Industrial Control Systems require a much more specialized set of skills to implement and maintain. For starters, the very environment of each are vastly different. IT networks are often climate-controlled office environments, whereas OT networks can be exposed to extreme elements and process environments.
More importantly, what sets OT professionals apart is their knowledge of how to implement specific industry processes, using a range of industrial controls across multiple platforms. Lastly, they must use this knowledge to make everything communicate in an efficient, reliable, and intuitive manner.
With vast experience across numerous industries, platforms, and technologies, Champion’s OT professionals deliver on this expertise.
Cost of Ownership
The natural lifecycle of IT versus OT lends itself to completely different budget approaches. While IT environments typically change every 12-18 months, OT environments can last 10-15 years or more – if they are properly designed and maintained. Therefore, planning for Total Cost of Ownership (TCO) takes not just different expertise but also a different approach and methodology to achieve a comprehensive cost.
The key to enabling Industrial Control Systems for extended durations is proper maintenance and support. In addition to cybersecurity risk mitigation, including budgetary funds for preventive maintenance and support is essential in any OT environment. As a system ages, it is key to provide regular security patches, scheduled backups, and a supply of spare parts to achieve the greatest production output.
Champion’s knowledge of these items, paired with our 24UP® Solutions, allow customers to tailor specific needs into one easily-predictable budgetary plan.
Compliance
Whether for the safety of workers, surrounding communities, or environment, compliance standards are often far more stringent on OT systems. Federal and state agencies regularly monitor and regulate industrial processes due to their inherent ability to impact the community at large.
Another unique difference between IT and OT is the types of compliance each must meet. Industrial Control processes are typically subject to far more scrutiny due to their ability to impact more than a corporate entity. If improperly maintained, a process can harm employees, communities, or the environment. For this reason, it is imperative that OT systems function correctly and reliably.
OT networks continuously monitor process stages, operating temperatures and pressures, environmental emissions, leaks, or any other number of factors associated with the facility. Reliable systems improve overall safety. They also allow companies to generate real-time or historical reports for compliance agencies like the EPA, DEQ, FDA, and OSHA.
Champion engineers and professionals hold the experience necessary to implement the reliable OT systems our customers demand.
Ready to learn more? Contact us today to schedule a no-cost consultation.
We empower our clients to build safe, sustainable operations by delivering comprehensive Operational Technology (OT) solutions. From concept to implementation and beyond– we'll be there every step of the way.
Let's collaborate.
Schedule a no-cost consultation today.
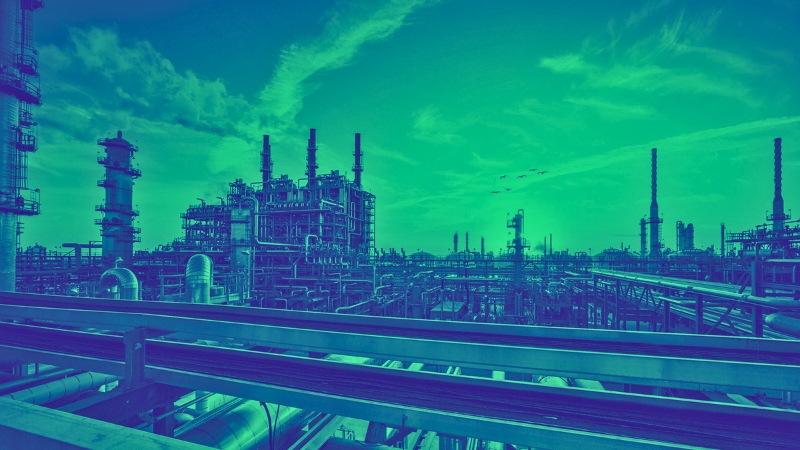
more on our website
Industrial Automation
More Posts