“My old control system is still hanging in there. How can I justify a costly replacement to management?” This is an age-old question, to which many believe: “If it ain’t broke, don’t fix it.” However, when it comes to Industrial Control Systems (ICS), this approach is often the riskier and costlier route for facilities.
The answer lies in Total Cost of Ownership (TCO) – a method of engineering, economic, and financial analysis. TCO aims to consider all of the direct and indirect costs related to a product over its lifetime. The TCO of your car isn’t just the purchase price, but all the related costs over the time you own it: gas, financing, insurance, maintenance, depreciation, and more. The same approach can be applied to a control system over its lifetime.
Common Hidden Costs
Maintenance
The cost of maintaining legacy systems grows exponentially with age. This is due to increased routine problems, along with added system complexity from customization and changes. Over time, updates become more time-consuming and costly.
Talent
In parallel with maintenance costs, talent costs are much higher on a legacy system. Not only are the costs exorbitant in man-hours, but unlike on newer systems, they often require skill sets that are expensive and difficult to find.
Support
As proprietary legacy systems reach a point of limited or discontinued vendor support, the costs of support begin to soar. Tie this to increasing talent costs for external support, longer support response times, and – dare we say it – interruptions in production that affect your bottom line at its core.
Compliance
With industry regulations continually changing, the cost of keeping legacy technology in compliance can be burdensome. Even more costly are the risks of noncompliance, with penalties or fines adding to your Total Cost of Ownership.
Lost Revenue Potential
Without newer features such as mobile data access, or the ability to gather and act via analytics tools, your plant operates on inefficient processes, lower production output, and results in a dwindling bottom line.
New Tech, New Benefits
Implementing new technology can bring a wealth of benefits, from risk reduction and meeting heightened regulatory standards to better decision-making and improved efficiency. Technology of today enables facilities to be more agile, innovative, and cost-effective in an ever-evolving climate.
Concerns of process interruptions can most times be eliminated using well-planned migration approaches, and increased security can alone make the switch a worthwhile investment. Champion’s Certified Cybersecurity Experts are trained in the latest ISA/IEC 62443 standards for Cybersecurity, ensuring your new system benefits from the most current, comprehensive safeguards.
At some point, legacy technology becomes a barrier to daily operations, business stability, and overall growth. By knowing the true cost of running legacy systems, industry leaders can see the clear return on investment (ROI) of embracing new technology and its upward-driving effects on your bottom line.
Ready to learn more? Contact us today to schedule a no-cost consultation.
We empower our clients to build safe, sustainable operations by delivering comprehensive Operational Technology (OT) solutions. From concept to implementation and beyond– we'll be there every step of the way.
Let's collaborate.
Schedule a no-cost consultation today.
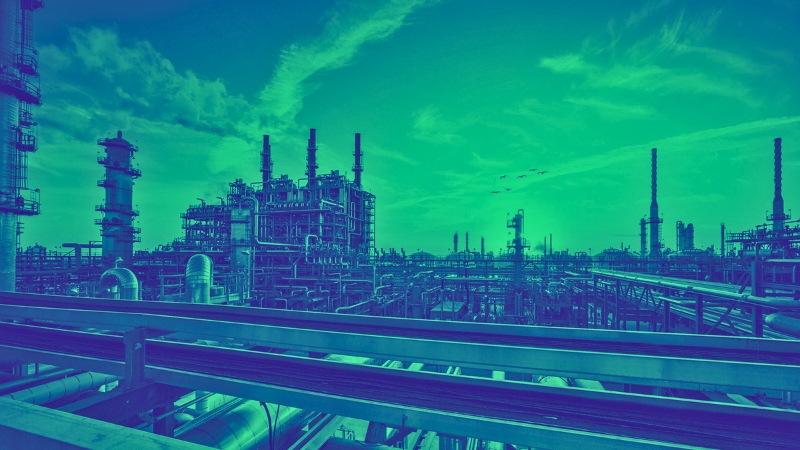
more on our website
Industrial Automation
More Posts